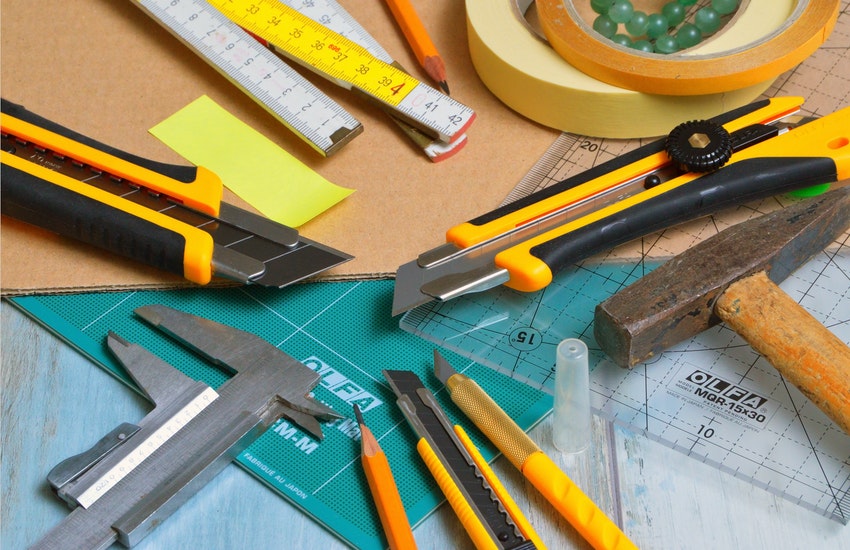
You can check the oil level in your air compressor with an oil level gauge. There is a dipstick on the oil cap in the crankcase if yours is a direct drive. Some of the bigger air compressors have site glass that makes it easier to check the oil level.
Turn it Off First
Turn the air compressor off before you check the oil level no matter what type it is. Due to the vibration and shaking, the oil is never at the rest. It can block your sight and the whole dipstick will be covered with oil as a result. There will be problems with opening the oil cap because oil may come out from the crankcase.
Check Oil Using a Dipstick
After turning off the equipment, open the oil cap. A dipstick will be attached to it. Take it out and clean the oil off with a towel or rag. Make sure the dipstick is clean. There are usually two marks on the dipstick. The bottom one shows the lower limit and the higher one represents the upper limit.
Check Oil via Site Glass
Usually, the site glass has a red, circular mark at the center. You can see the oil level between the center and the upper edge of the circle. If the limit is lower, the level will be at the center of the circular mark. If it’s on the upper edge of the mark, that means a higher limit.
If your site glass doesn’t have any marking on it, make sure that the oil level is between 2/3 and 1/3, around halfway for some compressor models. In this case, a lower limit would be 1/3 or 1/2 of the vertical length or height of the sight glass. The higher one would be 2/3 of the vertical length or height.
Why You Should Check the Oil Level Regularly
The crankcase needs constant lubrication because of the high friction between the many moving parts of an air compressor. That is why some air compressors use oil. According to AircompressorsUSA.Com, Oil also provides some degree of air tightness between the piston holes and the pistons.
Oil is gradually lost through the air intake hole and the exhaust when you use the compressor. We recommend checking the oil level each day before using the compressor because it is damaged if run without oil. Maintaining a consistent oil level is part of the good maintenance of a compressor. This ensures the longest possible life cycle.
At the same time, take care not to overfill the compressor with oil. Common issues resulting from this include oil leakage in the discharge or oil leakage through other parts. Excess oil is likely to burn, leading to an unpleasant smell. Finally, oil might be deposited in the tank.
How to Deal with Too Much Oil in the Air Compressor
If you’ve overfilled your compressor with oil, you have to remove it. There are two ways to do this. The first one is draining it via siphon pipe. To do this, the compressor needs to be above the floor. Insert one end of the pipe into the crankcase. The other end should be low enough so as to draw the oil out using the force of gravity.
The second option is using a sponge to seep the excess oil out from the crankcase by inserting it through the oil cap.
Prevent the Compressor from Running out of Oil
No air compressor can be continuously supplied with oil automatically. If you use it often, check the oil at least every day, on which you run it. If you only use it now and then, check the oil level before you turn it on.
Sometimes, your compressor will burn more oil than other times. This shows that something is wrong with it. This may be due to excessive heat or oil leakage. In such situations, talk to a mechanic or the manufacturer.
As a rule of thumb, maintain the exact oil level recommended by the manufacturer. You should change your compressor oil when it starts getting visibly dirty. Use 30W ISO 100 or 20W ISO 68 non-detergent oil unless the manufacturer recommends another one. The intervals of air compressor oil change vary depending on the machine. It’s every 3 months for reciprocating compressors, after 7000 hours of use for rotary screw compressors if you use standard oil and once every few months for food-grade oil. In every event, the compressor’s oil should be changed at least once a year.
Final Thoughts
Oil is important in the operation of any compressor as it serves to remove heat generated by the compression process. It also provides a seal in many designs. Oil lubricates the crank and wrist-pin bearings and the sidewalls of the cylinder in the case of piston compressors.
Rotary-vane compressors rely on oil to seal the minute space between the housing bore and the vane tips. Scroll compressors are known as oil-less because they do not normally use oil but, of course, their capacities are somewhat limited. Centrifugal compressors are in a different league than their positive-displacement brethren and do not introduce any oil into the compression stream.
Rings on the piston provide sealing of the compression chamber and control the passage of oil into it, as with piston engines. Rotary-screw compressors inject oil into the compressor body to both remove some of the heat of the compression process and seal the two non-contacting rotors.
Makers rely on several approaches to create oil-free compressors. Piston-compressor makers can employ one-piece piston-crank assemblies that ride the crankshaft on eccentric bearings. This design does away with a wrist-pin bearing on the piston. Piston-compressor manufacturers also use certain self-lubricating materials for the sealing rings and cylinder liners.
There are compromises to make whatever you choose. Some of the disadvantages of oil-less compressors are increased wear, more frequent maintenance, heat-management issues, and reduced capacity. An oil-based compressor is a good idea if it is acceptable to filter out oil or simply live with it.
To sum up, we recommend making a habit of checking the oil level. This will help you avoid any oil-related problems by maintaining proper oil levels.